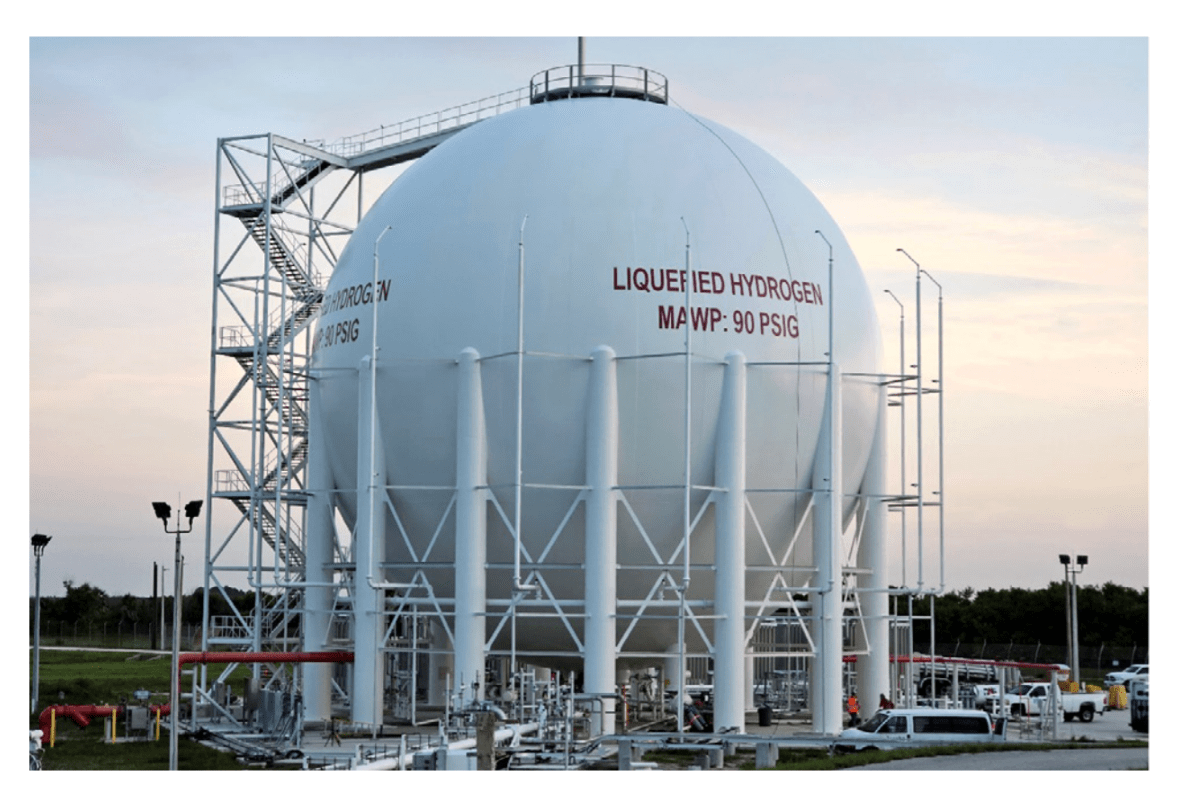
Helium Conservation by Diffusion Limited Purging of Liquid Hydrogen Tanks
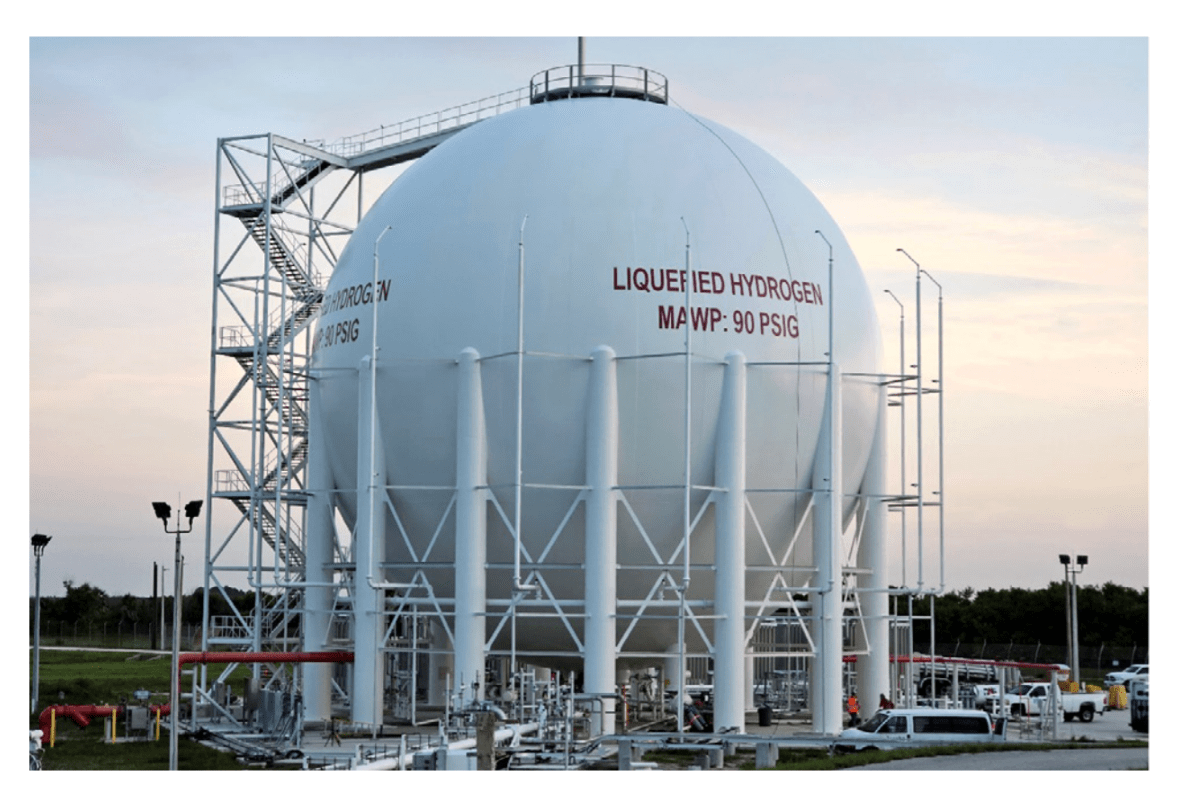
This article is from the 2024 Technical Update.
The NASA Engineering and Safety Center (NESC) has developed an analytical model that predicts diffusion between two gases during piston purging of liquid hydrogen (LH2) tanks. This model helps explain dramatic helium savings seen in a recent Kennedy Space Center (KSC) purge, shows that undesired turbulent mixing occurred in Space Shuttle External Tank purges, and is applicable to future helium purges of the Space Launch System Core Stage LH2 tanks.
Background
In 2023, work was completed on a new 1.3-million-gallon (174,000 standard cubic feet (scf)) liquid hydrogen tank at KSC in support of the Space Launch System[1], see Figure 1. Per contract, the vendor delivered this tank filled with gaseous nitrogen, leaving KSC ground operations the task of replacing the nitrogen with helium: a necessary step prior to introducing liquid hydrogen, which would freeze the nitrogen. Prior helium/nitrogen purges on the Apollo/Space Shuttle era 850,000-gallon (114000 scf) LH2 tanks were performed by pumping
out the nitrogen, introducing helium, drawing samples, and then repeating if necessary. However, the new tank did not have a vacuum port, so instead, it was decided to introduce the helium from the top of the tank and push the nitrogen out of the bottom. Two million scf of helium was obtained and made ready for fear the two gases would mix, resulting in a long and expensive purge. Surprisingly, this top-down, or piston purge, resulted in a rapid replacement of the nitrogen with helium, using only 406,000 scf of helium, about 1.6 million scf less than planned (at $1/scf this is a $1.6 million dollar savings). To better understand this remarkable result, the NESC was asked to address the questions; why did this work so well and can it be improved further?
Upon realizing that the purge was diffusion limited and could be modelled, variations were studied, leading to three important conclusions. The flow rate should be increased until the onset of turbulent mixing; once started, the purge should not be stopped because this allows additional diffusion to occur; and trying to improve the purge by varying temperature or pressure has little benefit. Purging of the huge LH2 spheres is rare, but purging of flight tanks is common. In 2008, purge data from three Space Shuttle External Tanks was measured using a mass spectrometer and the NESC was asked to apply the diffusion model to this data. Doing this showed
evidence that turbulent mixing occurred indicating that the flow rates needed to be decreased. Having such a model has provided insight into the use of piston-type helium purges at KSC, with the goal of saving helium and manpower. This work is now directly applicable to purging the LH2 tank on the Space Launch System Core Stage.
The Binary Gas Sensor
During past purges, gas samples were taken to a lab to indicate the status of the purge but doing that for a piston purge would introduce time delays, allowing unwanted diffusion to take place. Fortuitously, an independent NESC assessment[4] was evaluating a binary gas sensor, with an excellent combination of cost, size, power, and weight to implement in the field, providing rapid real-time monitoring of the purge gas ratio. Using this sensor made the piston purging of the new LH2 tank successful.
References
- Fesmire, J.; Swanger, A.; Jacobson, J; and Notardonato, W.: “Energy efficient
large-scale storage of liquid hydrogen,” In IOP Conference Series: Materials
Science and Engineering, vol. 1240, no. 1, p. 012088. IOP Publishing, 2022. - Youngquist, R.; Arkin C.; Nurge, M.; Captain, J.; Johnson, R.; and Singh, U.:
Helium Conservation by Diffusion Limited Purging of Liquid Hydrogen Tanks,
NASA/TM-20240007062, June 2024. - Singh, U.: Evaluation and Testing of Anaerobic Hydrogen Sensors for the
Exploration Ground Systems Program, NASA/TM-20240012664, Sept. 2024.